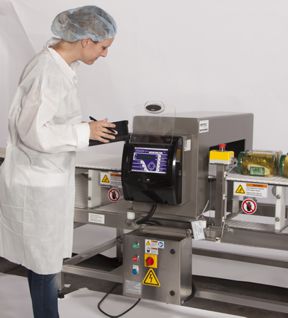
How To Pass a Detector Audit
July 1, 2019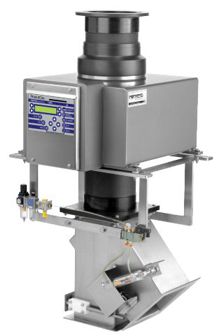
Gravity Fed, Conveyer Fed vs. Pipeline Metal Detection Systems Test Pieces
July 8, 2019Guide To Metal Detector Verification / Audit
From the outset, metal detector verification is absolutely vital! You need it to ensure that your company is adhering to food safety standards. This includes, of course, that your products are free from any contaminants. You have to consider the impact of contaminated product on your customer. And it’s important to acknowledge how much even a single recall caused by contamination can cost your company. It’s a loss in terms of money, time and public relations. So it is easy to see why maintaining the highest safety standards is so important.
HACCP Plans
According to your HACCP plan, you should employ a series of metal detectors at various points along the production line. This ensures that potential contaminants are detected and removed as early as possible. As it is not unusual for metal detectors to break down over time or lose their calibration. So it is essential to regularly test all detectors to determine whether they are functioning properly.
The HACCP requirements not only govern the use of metal detectors, they also contain specific guidelines for metal detector verification. Verification involves regular testing of all equipment to ensure that automatic rejection of contaminated products is occurring. If metal detectors are operating correctly, they should detect the presence of specially designed test pieces and reject them.
Placement
Metal detectors can be placed toward the beginning of the production line to test incoming ingredients. Throughout the line they can test the product as it is handled. Toward the end of the line, after the product has been packaged. By performing tests at each step, the overall quality of the final product can be verified and potential risks minimized.
Verification
Without a doubt, the validity of any test results is dependent on a number of factors. This includes the careful calibration (to your product) of all metal detectors and the quality of the test pieces used. Test pieces come in a variety of sizes and shapes to fit any particular product. For proper metal detector verification, test pieces should be incorporated into your product and fit the aperture of your detector.
Remember, verification also depends on the regularity of testing. All metal detectors should be tested at the beginning of each shift and when there is a change of products. Ideally, the interval between tests should be short. Then, if an error occurs or a contamination found, it can be corrected quickly. Any potentially affected products can be recalled before leaving the facility.
Test Pieces
Proper metal detector verification requires the use of test pieces in various compositions, including ferrous, non-ferrous and stainless steel. Regal Packaging Services provides high quality test pieces in all of these materials designed to fit each customer’s individual needs. And we offer cards, sticks, rods, pipes and other unique shapes and certify each individual test piece to ensure durability.
When it comes to your products, safety is key! That’s why regular metal detector verification should be a vital part of your company’s practices. With test pieces from Regal Packaging you are assured you have everything needed to verify your metal detector’s operation. That kind of confidence is hard to come by, but Regal Packaging can make it a reality for you and your customers.