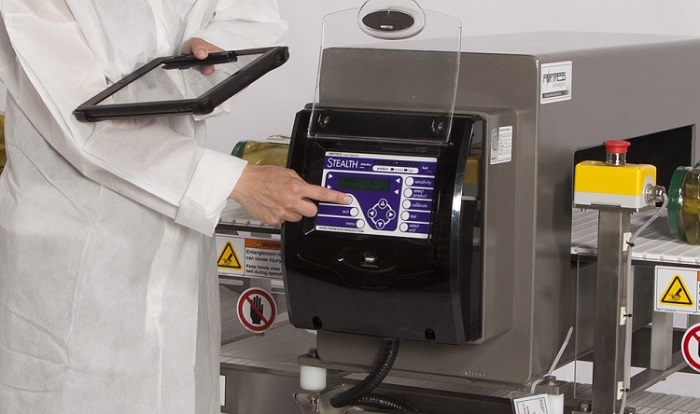
Why Use a Metal Detector and Its Test Pieces In The Food Industry?
April 5, 2018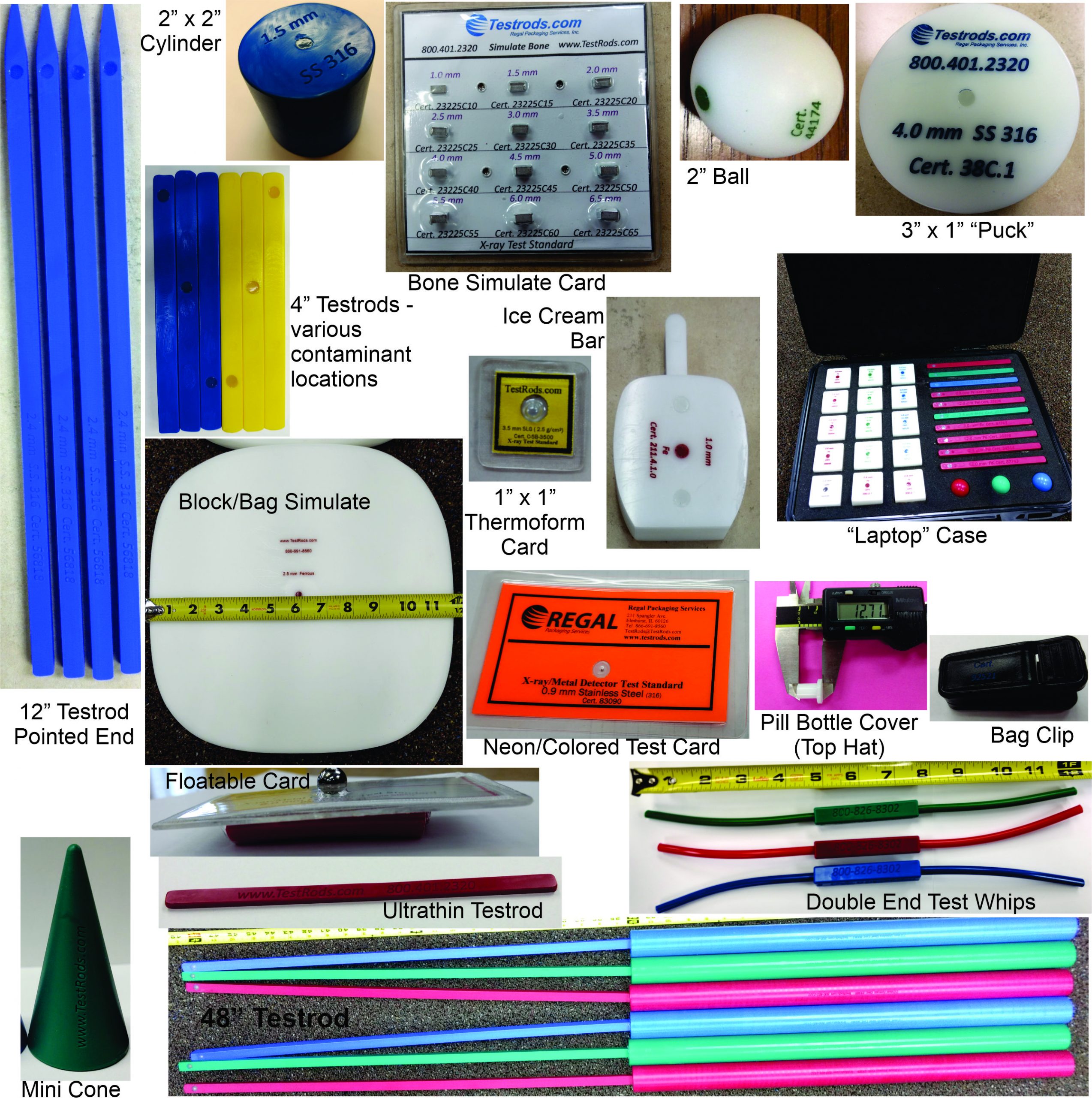
Give Yourself Peace of Mind With Metal Detection Test Pieces
July 3, 2018
Using Metal Detection Test Pieces in the Food Industry Helps Put Safety First
With the use of metal detection test pieces in the food industry, food executives and workers show they put safety first. And that should make consumers feel better. Food product manufacturers need to ensure that their products contain no contaminants. This has become more important in recent years. There are always new instances of food tampering, and food safety issues seem to spring up almost every day.
Using a metal detector may seem like an unusual step in the food industry. Pieces of metal should not be an immediate cause for concern, you might think. But any time you have a processing plant where complicated pieces of equipment are regularly used, anything is possible.
Assumptions and Response
The obvious assumption, in this case, is that manufacturing plants should be adhering to strict health and safety standards. This would render this kind of extra precaution unnecessary, but that is not true. The fact is, even the most well-run facility may occasionally have problems with contaminants accidentally falling through the cracks, literally.
The automatic response, then, is to ask where is the contamination coming from? And how would the use of test pieces in the food industry help to prevent it? Unclean working conditions can certainly be a source of the problem, but that is not always the case. In most cases, contamination is actually caused by the regular degradation of manufacturing equipment. Any time you have metal machinery in regular use, the metal will naturally wear down or break apart over time. That can result in tiny metal particles falling into the food being processed.
The Solution
The best way to counter this is by using metal detectors to locate these particles before the food ships. Food production usually involves the use of a multi-step conveyor system. It is necessary, then, to use a metal detector at various steps along the way. Ideally, at the the end of this process as well. In this way, each food item can be carefully scanned to detect the presence of any contaminants. If a foreign substance were found, the entire product would be rejected before it ends up on store shelves.
In general, metal detectors in the food industry use one of two processes: either “balanced coil” or magnetic field detection. A series of coils scan foods, the first coil illuminating any contaminants and the second and third coils detecting them. With a magnetic field system, contaminants are magnetized and then detected by coils. In either case, the test pieces in the food industry is critical.
Testing
As with any type of machinery, it is extremely important that metal detectors be tested regularly to make sure they are functioning correctly. This is done by using test pieces made of food grade plastic with small pieces of metal embedded in them. The test pieces are available in various sizes and materials to accommodate different types of equipment.
Test pieces in the food industry are placed within a group of finished products to ensure proper function, which is then passed through the equipment. If the machinery is working correctly, it should detect the metal in the test pieces. To be doubly sure, you should run the test pieces through the process twice, once at the front of the group of products and once toward the end.
Regal Packaging Services provides top quality metal detection test pieces food industry professionals can rely on. Each piece is manufactured with care and certified so our customers can rest assured that they are getting the best quality product, formulated to meet the specific standards of the food industry. Certificates are complimentary and never expire.
Since we know machinery can differ from one company to another, we also customize pieces to fit our customer’s specifications. If you can imagine it, Regal can design and manufacture it. You cannot afford to take chances with your customers and neither can we; that is why Regal goes out of its way to provide only the best test pieces in the food industry to help keep your metal detectors running smoothly.
2 Comments
I ate a 1/2 of a sponge cupcake and noticed there was a piece of curly stainless steel piece on the remaining cupcake that looks like it’s from a scrubber. What kind of tests would I need to ensure that I’m not contaminated with any type of health risks?!? Thanks!!!
Linda,
Thanks so much for your question.
Wire is a difficult challenge for metal detectors.
Are you asking the question for a company or as a consumer?
All food plants are required to run food through a metal detector or x-ray inspection system.
These detectors are usually capable of finding metals 1.0mm in size and sometimes even smaller.
Wire is difficult because as it passes through a metal detector, it’s possible that its orientation can “fool” the detector into believing nothing is there.
Its an uncommon issue, so it’s rare that you ran into the issue.
I would contact the cupcake company if you can and let them know what happened.
Most likely, they can take that information and make changes as needed on their production line to mitigate against further issues.
The vast majority of food processors or manufacturers are very careful and concerned that what happened to you doesn’t ever happen again.
It’s in the best interest of their customers and for them as a company.
I hope that answers your question. Feel free to contact me if you have further questions.