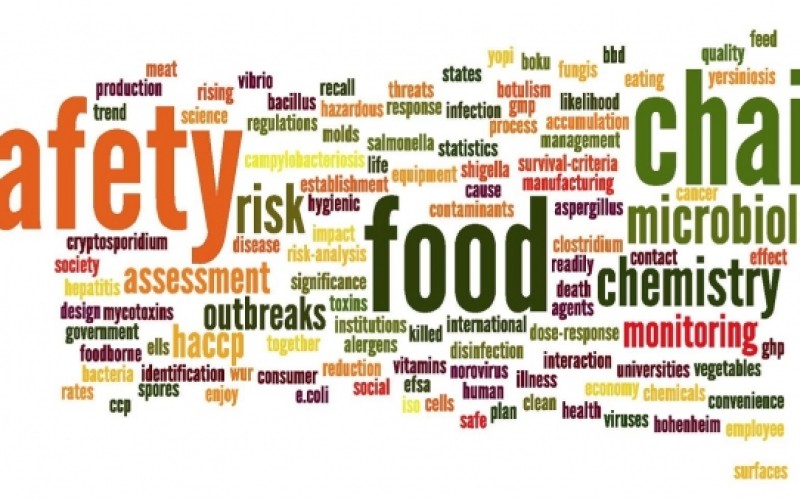
Best Practices For Metal Detection In The Food Industry
June 17, 2019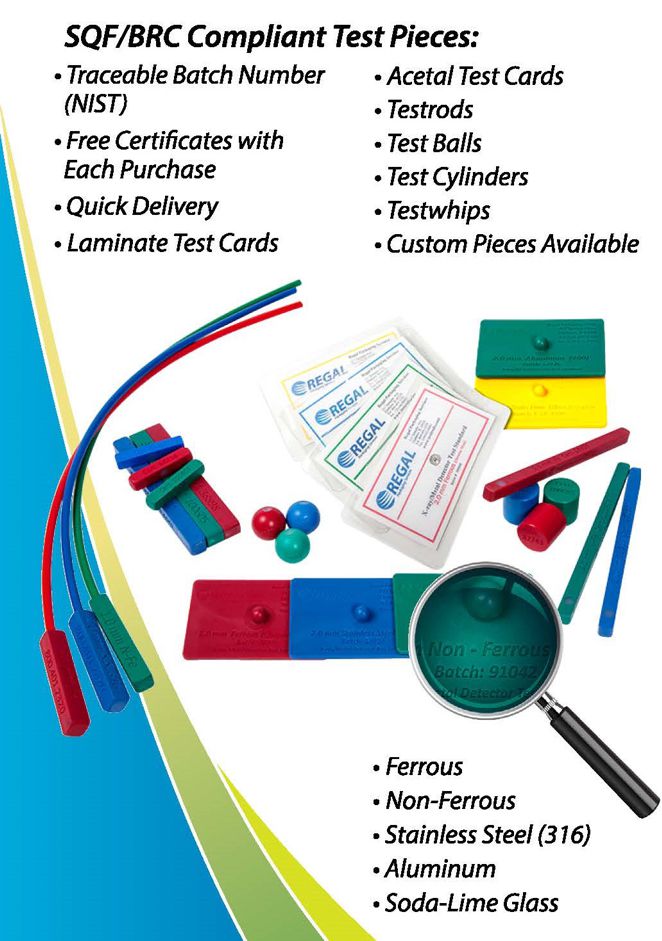
Using Metal Detector Test Pieces
June 24, 2019Compare Food Grade Metal Detectors
Food grade metal detectors come in many different types, from conveyors to pipelines to gravity feed. Choosing the right detector for your business can be critical and may depend on various factors. You will have to consider the type of product you’re manufacturing and the type of packaging you use. Consider your options carefully before making a choice. You need to ensure that you are best able to comply with the government’s ever-tightening food safety guidelines.
Food safety is not something to be taken lightly. Even one contaminated product reaching store shelves can have a disastrous effect both from a financial and PR perspective. This is why food safety guidelines are in place and why metal detection systems have become standard in the industry.
Detector Types
There are two basic types of detection systems: metal detectors and x-ray systems. Food grade metal detectors are used to identify the presence of all types of metals within food products. An x-ray system can be employed to detect other types of contaminants, including glass, stone and plastics. Many manufacturers opt to employ a combination of both for maximum safety.
In terms of metal detectors, the different types are used to inspect different types of products. For most packaged products, conveyer systems are ideal. In all instances, the detector uses a series of coils to produce magnetic fields. Then these fields identify the presence of a contaminant within a product. The system then automatically rejects the package once contamination is confirmed. If the packaging is metalized, then a detector that employs magnets can be utilized instead.
For non-packaged products, a company may require the use of other types of food grade metal detectors. Vertical detectors can scan loose (i.e. powdered) products. Usually, this happens as product is pumped into bags. Pipeline systems detect contaminants in liquids and soft, dense materials like sausages and cheeses. The contaminated products are then channeled into isolation bins to remove them from the production line.
No matter which type of detector you use, it is crucial to perform regular tests to ensure that it is working properly. Tests are performed by inserting a specially designed test piece into the production line. This should happen either within a sample pack of the product or directly in the flow of loose, unpackaged product. If the detector is working properly, it should identify and reject the test sample.
Safety
Ensuring the accuracy of your food grade metal detectors is necessary for adhering to food safety guidelines. You should employ only the best quality test pieces such as those designed and created by Regal Packaging Services, Inc. We provide each customer with test pieces to meet the individual specification of their system. And we certify each individual piece to guarantee quality and durability.
Safety is paramount in the food industry, and that means employing the best metal detectors and testing them regularly. With high quality test pieces from Regal Packaging Services you can be sure that your metal detectors are always functioning at their best and that your business is protected. When it comes to food grade metal detectors, peace of mind like that is something you just can’t put a value on.