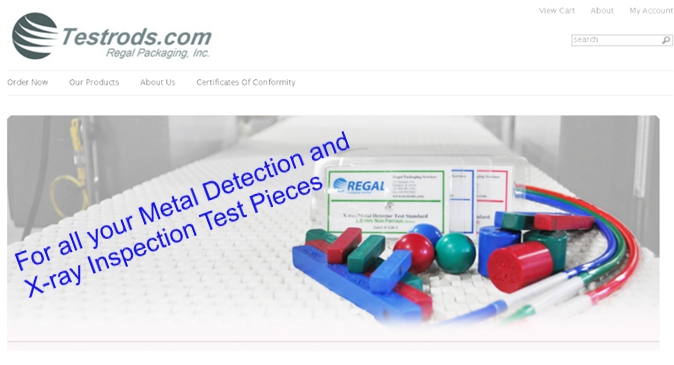
X-Ray Systems Test Pieces
June 12, 2019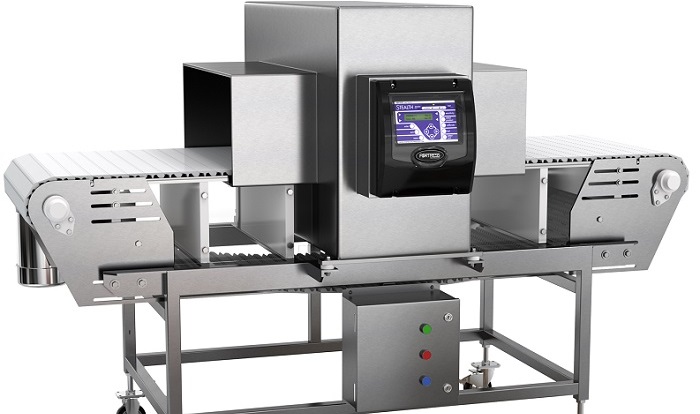
Compare Food Grade Metal Detectors
June 20, 2019Best Practices For Metal Detection In The Food Industry
Metal detection in the food industry is a critical step in adhering to strict food safety guidelines. Even a single contaminated product that reaches the marketplace can have a disastrous effect on your company. So naturally, it is in your best interest to prevent it. To begin, you can ensure the safety of your products by implementing HACCP plans. Then, include the use of best practices for metal detection and/or x-ray inspection systems. Follow these with regular testing to ensure your systems are functioning properly.
Within the food industry, there is a generally accepted set of best practices for metal detection that should be followed. Doing so will help guarantee safety. These principles involve choosing the proper type of metal detectors and incorporating them into your production line correctly. Testing them on a regular basis using high quality test pieces is crucial as well. These practices should be known and followed by all employees. A good food manufacturer will create a culture of safety.
Depending on the type of product you are manufacturing, you can choose from conveyor mounted, vertical or pipeline detectors. In general, conveyors are used for testing packaged goods. Vertical detectors for loose goods like snacks that are pumped into bags. Finally, pipelines are used for liquids or loose, dense solids like meats and cheeses.
Detector Placement
No matter which type you use, your detectors should be placed at Critical Control Points (CCP). This may be either after or near the end of the packaging process and should include an automatic rejection system. This way, if a contaminant is detected within an individual package, it will be instantly removed from the production line. This safeguards the company and customer before anything can be shipped. There should also be some sort of alarm to indicate when the rejection bin is full.
Adjusting the sensitivity of your detector is crucial to ensure accuracy. As part of the best practices for metal detection in the food industry, it is essential that the sensitivity of your detector be set for the conductivity of your product and readjusted when running different products. Also, if you move your equipment within your facility, you may need to check and readjust the sensitivity and calibration relative to the product effect.
Testing
Equally important is following a schedule of regular tests. This demonstrates that your detectors are operating properly and you are adhering to best practices for metal detection. Ideally, testing should be done on a consistent, diligent basis. You should always work to perform testing at short intervals. Then, if a contamination is found, potentially affected products can be recalled before leaving the facility. At the very least, it should be done at the beginning of each shift and between each change of product.
Metal detection in the food industry necessitates the use of quality test pieces in a number of sizes and compositions. This will include, including ferrous, non-ferrous and stainless steel. Regal Packaging Services provides pieces in a wide variety of shapes. There are cards (laminate, acetal and thermoform), sticks (rods), whips and cylinders to name a few. And 10 different contaminant materials include: Ferrous, Non-Ferrous, Stainless Steel 316, Soda-Lime Glass, Ceramic and Rubber. We work with each customer to meet their particular needs and certify each individual test piece to meet industry requirements.
You can’t afford to take chances when it comes to the safety of your customers and that means ensuring the quality of your products. With carefully designed and manufactured test pieces from Regal Packaging Services (Testrods.com) you’ll be able to keep your metal detectors working properly and know that you’re giving your customers only the very best. That’s quality you can depend on and results that you can trust. And following best practice for metal detection gives your customer confidence in your product and company.