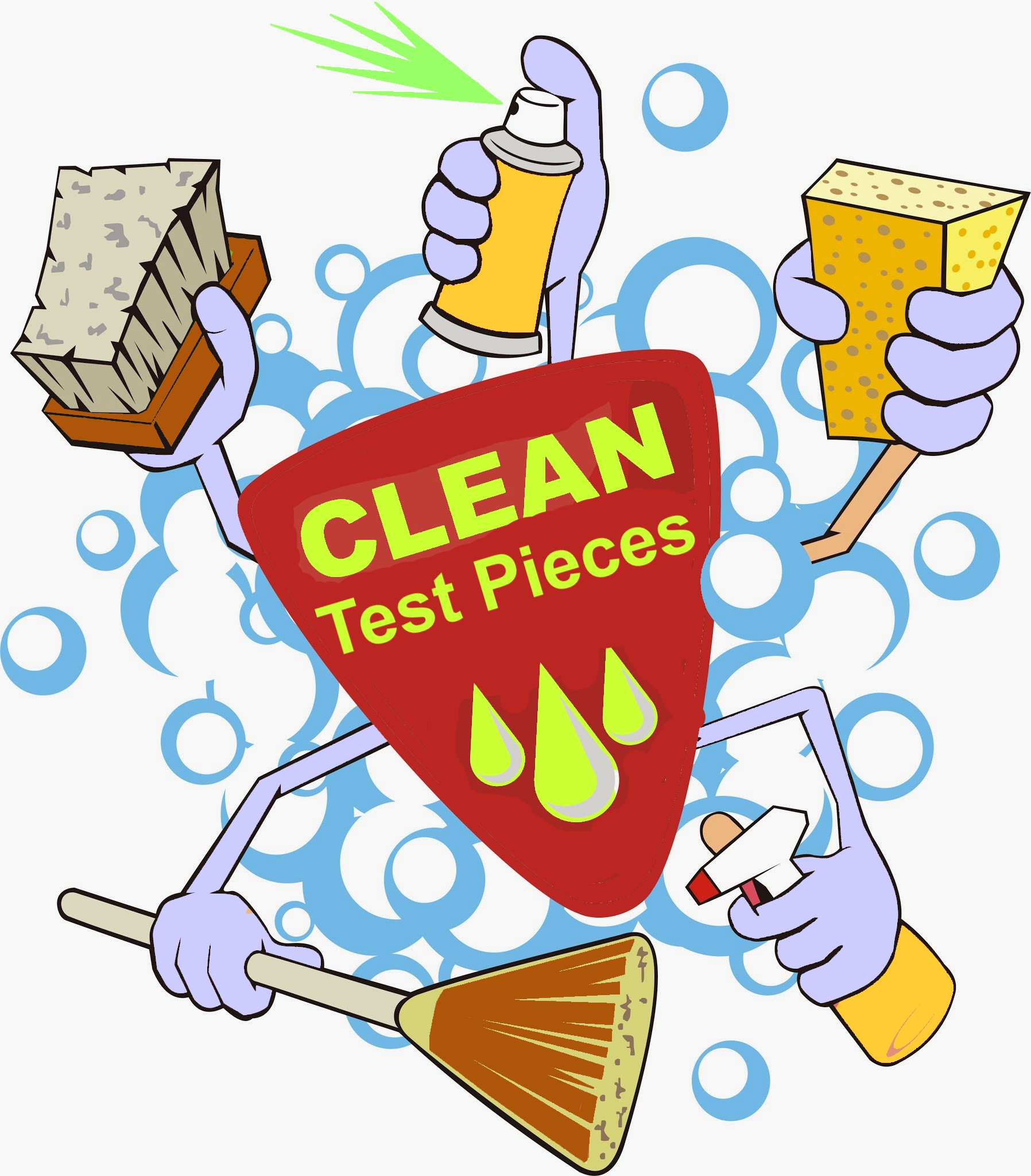
Cleaning Test Pieces
February 14, 2023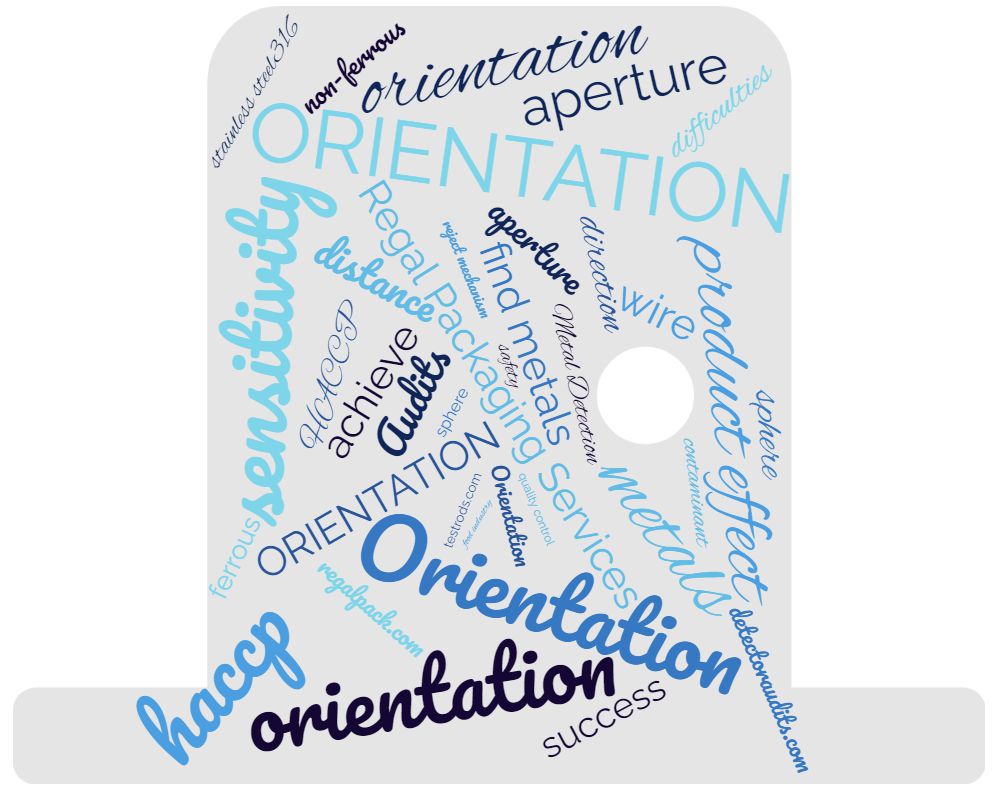
Orientation and Metal Detection are Key to Success
June 20, 2023
Complimentary Aspects of Contaminant Detection Systems
The continuing development of inline food inspection technologies means that the discovery of a broad spectrum of contaminants is achievable using either x-ray, metal detectors or magnets. Selecting the technology for a specific application will have a substantial influence on the safety of your end-product. Simply stated, there are complimentary aspects of contaminant detection systems.
The three technologies available for contaminant detection and removal are not necessarily in competition with one another. In fact, they are complementary to one another. Each inspection system type has its place in the process line and benefits for the extraction of foreign material.
Magnets are used “pre-packaging.” They function best on free-flowing bulk type products. Contaminants must come in contact with the magnetic fields and therefore require product passing through the magnet to be uninhibited in its flow characteristics. (You cannot choke fill a magnet). The ferrous metal particles must be pulled through the product onto the magnetic bars where they will be held until cleaned or released. A magnet can detect smaller pieces of ferrous metal than either x-ray or metal detectors.
A good location for magnets are in bulk-handling lines/railcar load-outs and incoming truck load-out areas.
X-ray systems work on the principle of measuring density. Two major factors determine detection capabilities of an X-ray system. They are the product over-all density and the uniformity of the density signature. The more dense the product, the less sensitive the system becomes. The more complex the density signature, the less sensitive the system becomes.
X-ray technology, as you might expect, is able to detect metal and some non-metal contaminants. In general, since most food products have an atomic density that is close to water (1), If the contaminant floats in water it is not detectable with x-ray. Contaminants such as hair, plastics, wood, fruit pits and metal foil are all examples of contaminants that are not detectable with x-ray.
Some application specific x-ray systems can also perform a variety of in-line quality checks. These applications are far and few between and using other “technology specific techniques” usually surpassing and x-ray system with these application specific requirements.
An X-ray system excels in applications when a known contaminant is integral to the product being produced. Such as bone/meat, stones/nuts, metal/foil pouches. In some cases, an x-ray system can outperform a metal detector in the detection of metal contaminants. But is rarely the reason to invest in an x-ray system. An x-ray system can detect dense material in foil pouches and therefore has an advantage over metal detectors on these types of finished packages. Also, since x-ray systems measure detection based on density, product conductivity would no longer impede detectability. An x-ray system is limited by the product being produced (too light weight/too heavy weight/complex radiographic image/free flowing products). Not all metals are detected by X-ray, Aluminum has low density characteristics and aluminum foil is not detectable.
A good location for an x-ray system is when a contaminant is integral to the product or when the product/packaging inhibits the use of a metal detector.
A metal detector can detect all metals based on their conductive and or magnetic properties. Detection levels, like X-ray and Magnets are still application specific. A metal detector can be used in almost any configuration (gravity/pipeline/conveyor). There is no limit to the size product that can be run through a metal detector. As long as metal is not integral to the product (metalized film/foil packaging) a metal detectors can be used in almost any application.
A good location for metal detector is when the product or packaging will allow for its use. Products in bulk, packaged or un-packaged products can all be inspected with a metal detector for the detection of metal.
Metal detectors/magnets/x-ray system are complementary contaminant detection devices. Each application will dictate the device type used. And in most cases they ALL could all be used in various locations within the plant to ensure that the “best” is being done to control foreign material from getting into your product.
So, given that there are complimentary aspects of contaminant detection systems, at Testrods.com, we offer 18 contaminants that can be used for x-ray inspection*:
Polypropylene | 0.9 g/cm3 | Borosilicate Glass | 2.23 g/cm3 |
Nylon | 1.1 g/cm3 | Soda-Lime Glass | 2.5g/cm3 |
EPDM Rubber | 1.14 g/cm3 | Aluminum | 2.7g/cm3 |
Buna Rubber | 1.2g/cm3 | Ceramic AL203 | 3.9 g/cm3 |
PVC | 1.41 g/cm3 | Ceramic ZrO2 | 6.30g/cm3 |
Delrin (Acetal) | 1.4g/cm3 | Stainless Steel 316 | 7.82g/cm3 |
Viton Rubber | 1.85g/cm3 | Ferrous (Chrome Steel) | 7.85g/cm3 |
PTFE (Teflon) | 2.2g/cm3 | Non-Ferrous (Brass) | 8.48g/cm3 |
Fused (Synthetic) Quartz | 2.2g/cm3 | Bone | similar to aluminum |
Knowing that complimentary aspects of contaminant detection systems, here at Regal, we specialize in an application specific approach to contaminant detection equipment. Regal Packaging Services represents Fortress Technology in Illinois, Wisconsin, Indiana and Iowa. We can help you determine which type technology is best for your application. Our goal is not just sales; we bring a great deal of knowledge, experience and service to the table. Our goal, ultimately, is the same as yours – to put quality, safe products on the marketplace. Give us a call at 630-942-8461 or email regalpack@regalpack.com. If it’s test pieces you need, visit us at Testrods.com, call 866-691-8560 or email testrods@testrods.com.