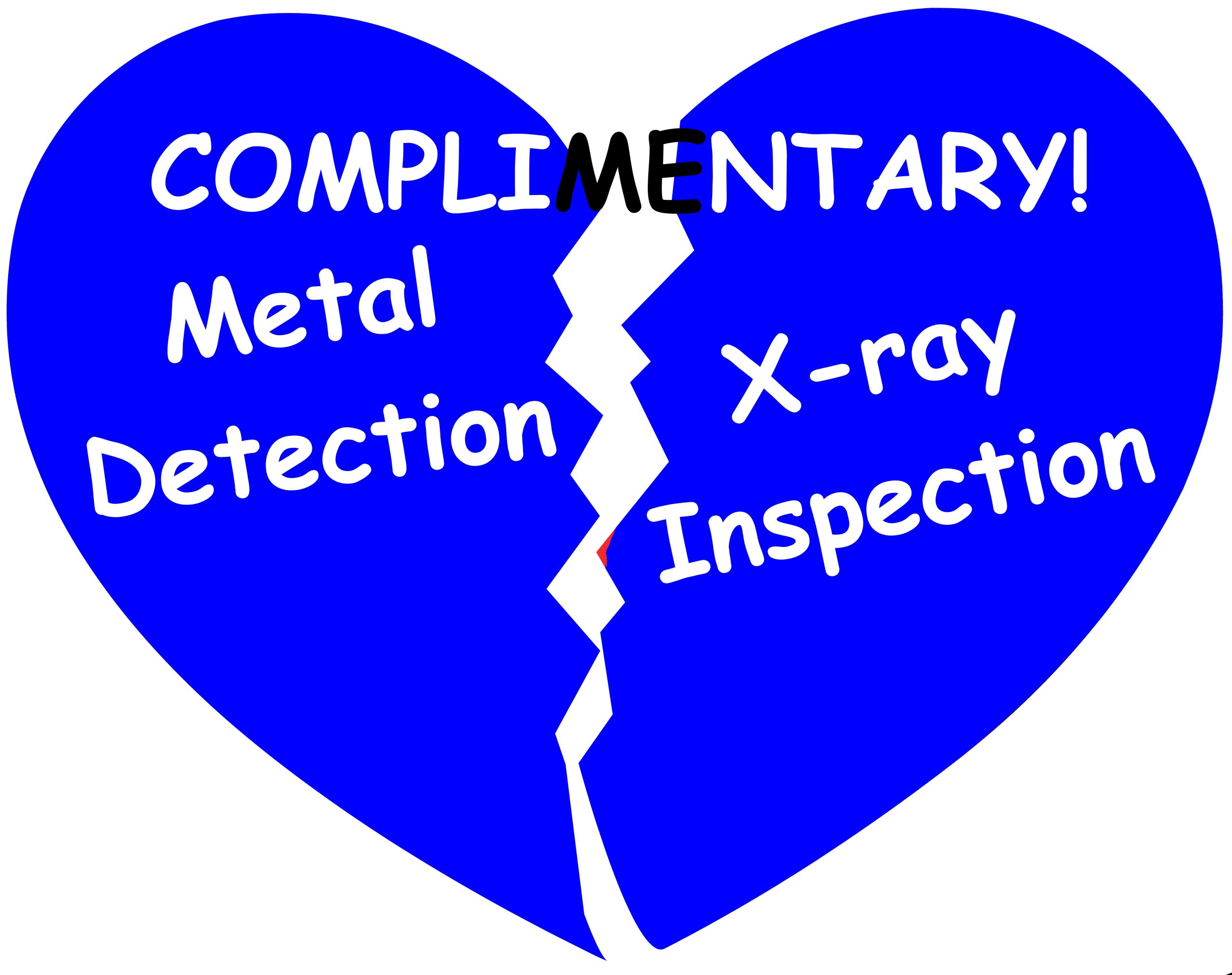
Complimentary Aspects of Contaminant Detection Systems
April 10, 2023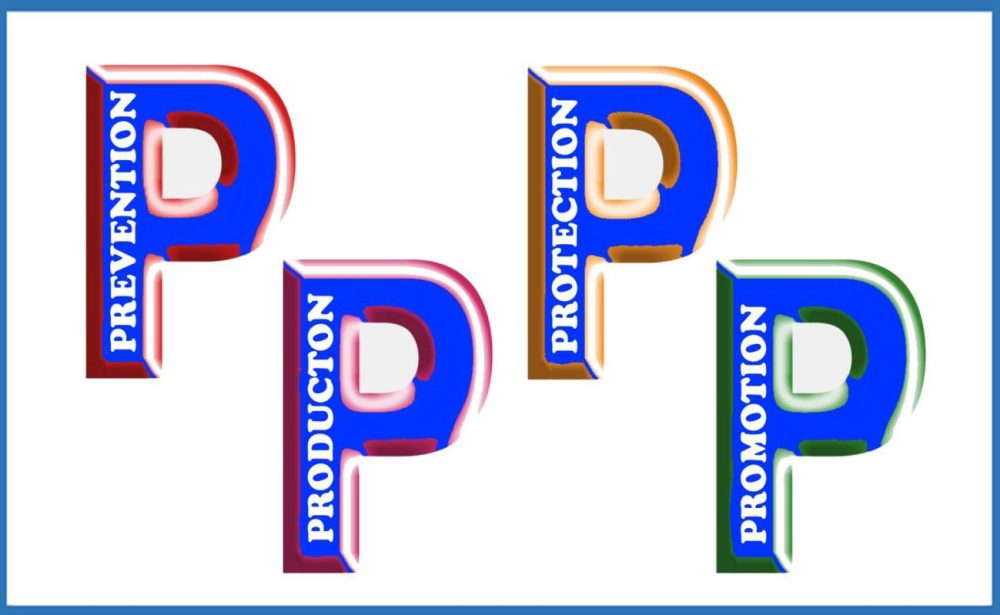
4 Critical Principles of Metal Detection
July 1, 2023
ORIENTATION AND METAL DETECTION
The relationship between orientation and metal detection is key to your success. If you’ve ever wondered why metal detection standards are predicated on spheres, it is because spheres are the same shape no matter how you look at them. In other words, they look the same from any angle and their shape never changes. Unfortunately, a contaminant (the metal you are trying to detect) is rarely (if ever) spherical, and it will produce a conductive signal dependent on its orientation as it is conveyed through the aperture. The most dramatic example, and perhaps the most difficult to achieve, is wire contaminants.
As you might expect, wire will produce a different signal than a sphere, and, again, this is partly due to its orientation when passing through the aperture.
Let’s take a look at this unique relationship between orientation and metal detection. Orientation and metal types cause the electromagnetic signal produced by wire shapes to vary greatly. In a worst-case scenario, a wire could produce a signal no greater than a sphere the same size as the diameter of the wire.
A wire (with thickness of 0.3mm), passing through the aperture in a particular orientation, may only produce a signal equal to a 0.3mm sphere. So if you are using 0.5mm as your achievement and rejection goal, the wire may pass right by undetected.
The diagram shown here demonstrates the different angles at which a piece of wire might travel through the aperture. Configuration “A” produces the strongest signal (most detectable), in ferrous-type wires. Angle “B” and “C” create the smallest signal (least detectable in ferrous). However, in non-ferrous and stainless steel 316 wires, the opposite is true. “A” provides the least signal while “B” and “C” provide the biggest signal.
It might be said that metal detectors view and detect the surface area of the contaminant relative to the aperture. Having said that, a sizable influence must be taken into consideration regarding your choice of metal sizes that will set the mark as your standard. As an example, logically, you might assume that a 1.0mm ferrous sphere is fifty percent as large as a 2.0mm ferrous sphere. Mathematically speaking, however, a 1.0mm sphere has a surface area of 3.14mm2 while a 2.0mm sphere has a surface area of 12.57mm2. The 2.0mm sphere, then, will be 4 times easier to detect.*
In essence, if the contaminant’s cross-sectional area is less than the metal detector’s sensitivity as it relates to a testing sphere, then that impurity will pass through without detection and, of course, not get rejected. This is part of the reason why it’s so critical to get the best results out of your metal detector and write your HACCP accordingly.
Orientation is also important as you consider how to position your product as it passes through the aperture. The larger the deviation in product effect, the less sensitive your detector will be, and the orientation of the product in the aperture can alter product effect. Imagine the difference between throwing a pebble in a glass smooth lake and doing a cannonball off the dock. The splash is the Product Effect. Upon entering the magnetic field of the detector, the product creates a ‘splash’ in the field.
Given that metal detectors function on a balanced field principle, the amount of ‘splash’ is what determines whether a metal detector is seeing product effect, or product effect AND contaminant. So be sure to calibrate the detector not only to the product (which is the only kind of calibration to be done on a metal detector) but to the manner in which the product will flow through the detector. If you have a rectangular product, for instance, and you calibrate it to the long edge then run it through the aperture along the short edge, you may get very different results.
Orientation and metal detection will always be have a very important relationship and should be included in a HACCP. You need to know your product and the contaminant types and size you hope to achieve if you’re going to be successful at eliminating hazards to the consumer.
* This is a head to head comparison, not taking into account any product effect or other variables.